αSTEP AZ Series Development Behind the Scenes: 10 Years of Progress and Future Prospects in Developing the World's Easiest Positioning Motor
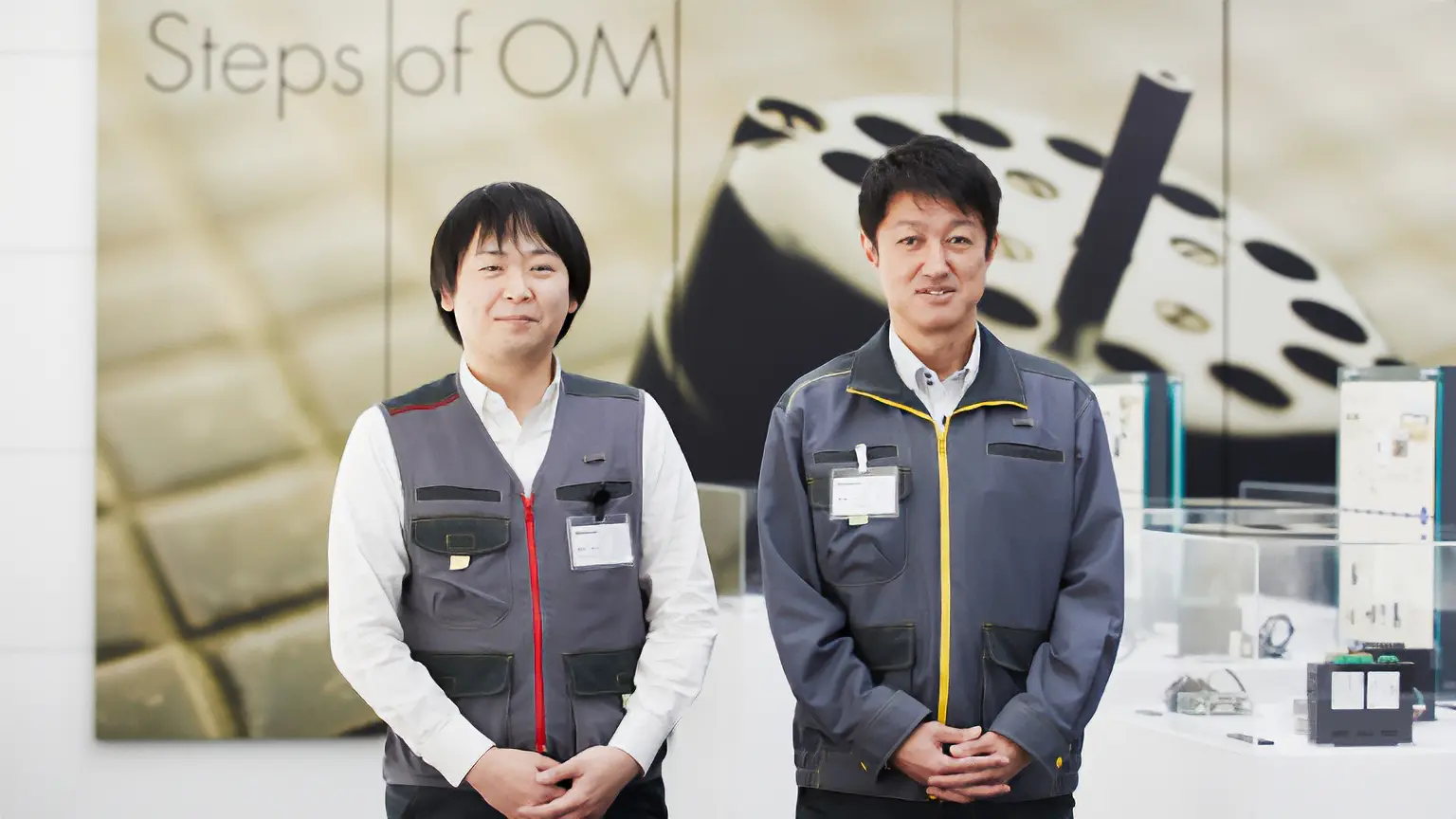
The αSTEP AZ Series incorporates ABZO (Absolute) sensors into stepper motors, achieving the construction of a battery-less absolute system. We have been able to reach our 10th anniversary with the support of many customers. And in January 2023, the servo-type AZX Series made its debut. To mark the milestone of the 10th anniversary and the release of the new AZX Series, we spoke to the developers about the evolving AZ family."
Chapter 1. On the Eve of the Birth of the αSTEP AZ Series
Drawing inspiration from the technology of miniaturizing encoders, a groundbreaking product was born.
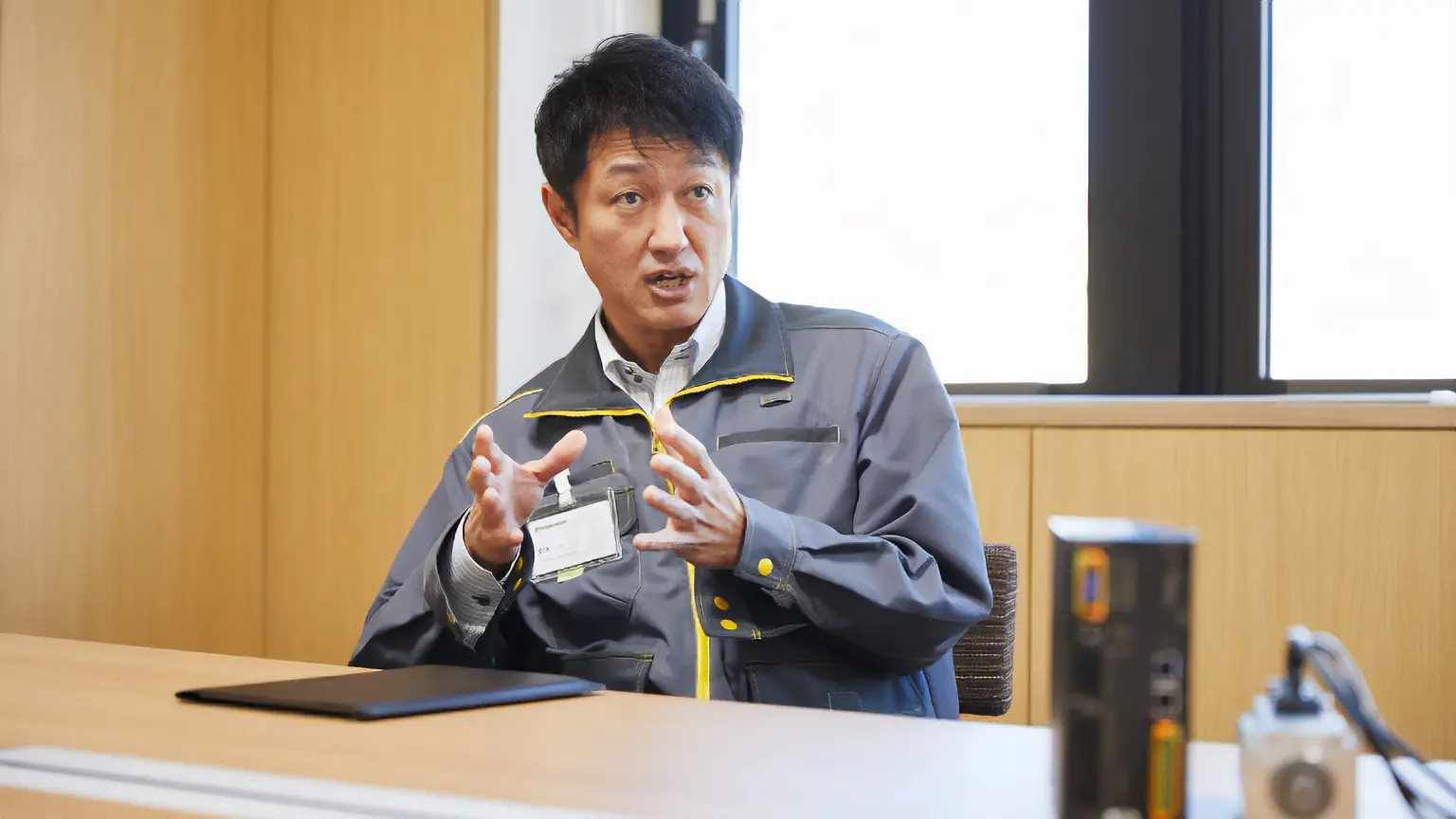
Could you please share the background and inspiration that led to the development of the αSTEP AZ Series?
Sugawara:Around 2010, there were advancements in the component technology that allowed for smaller mechanical absolute encoders. The initial spark for the αSTEP series came when the idea emerged that combining this technology with αSTEP could result in something interesting. While other companies also have battery-less absolute systems, it is common for them to be attached to servo motors. If attached to a stepper motor, it seemed possible to create a product where adjustments such as gain and the essential battery maintenance in absolute systems would not be necessary. Thus began the development of the AZ series. However, everything came to a halt due to the Great East Japan Earthquake in 2011. First, we prioritized supply responses. At that time, the economy was in a downturn, and the situation was such that we couldn't afford overtime. However, we continued the development in secret.
Suzuki:We gradually worked on the circuits in between our main responsibilities. There were also times when we had meetings on the train after returning from business trips. We made quite a few prototypes, probably more than other products.
During the product development, what kind of research did you conduct?
Sugawara:I accompanied customers to introduce the previous generation αSTEP AR Series, engaging in in-depth discussions and thorough hearing sessions to understand their opinions and challenges. Absolute encoders require a return-to-home operation when the battery runs out. For this reason, it was necessary to install an external sensor that is not usually used for recovery purposes, and challenges arose where the benefits of absolute encoders could not be fully utilized. We also found that there were challenges in setting the home position. With the AZ Series, we felt that we could solve these challenges from the development stage, so there was a sense that this could work.
In the development of the AZ Series, were there any technical challenges or difficulties that you encountered?
Sugawara: The sensor part was indeed challenging. It was indeed the absolute encoder part. Being a mechanical absolute encoder, it involves combining gears internally. Ensuring the accuracy and reliability of that mechanism was crucial. We had challenges, such as repeating tests that we had never done before. However, since we also handle in-house production of reducers, I believe we were able to leverage the gear technology and experience we have cultivated in that area.
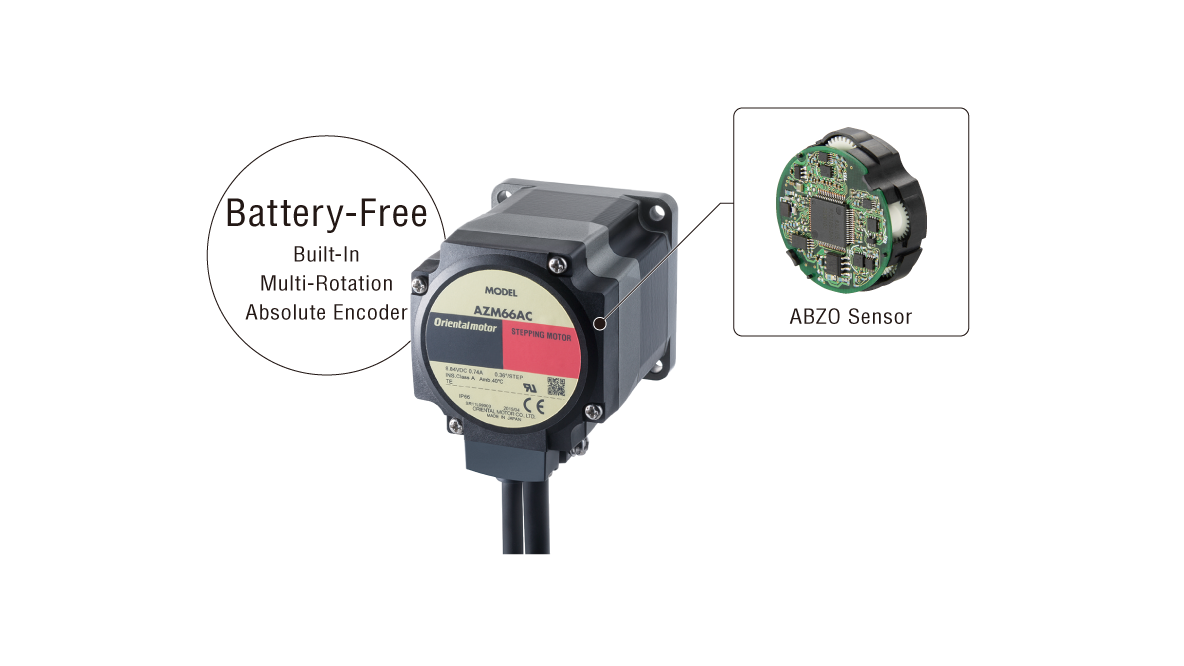
Chapter 2. Achieving Evaluations Beyond Expectations
Solving the customer's return-to-home challenges and gaining penetration along with a comprehensive lineup.
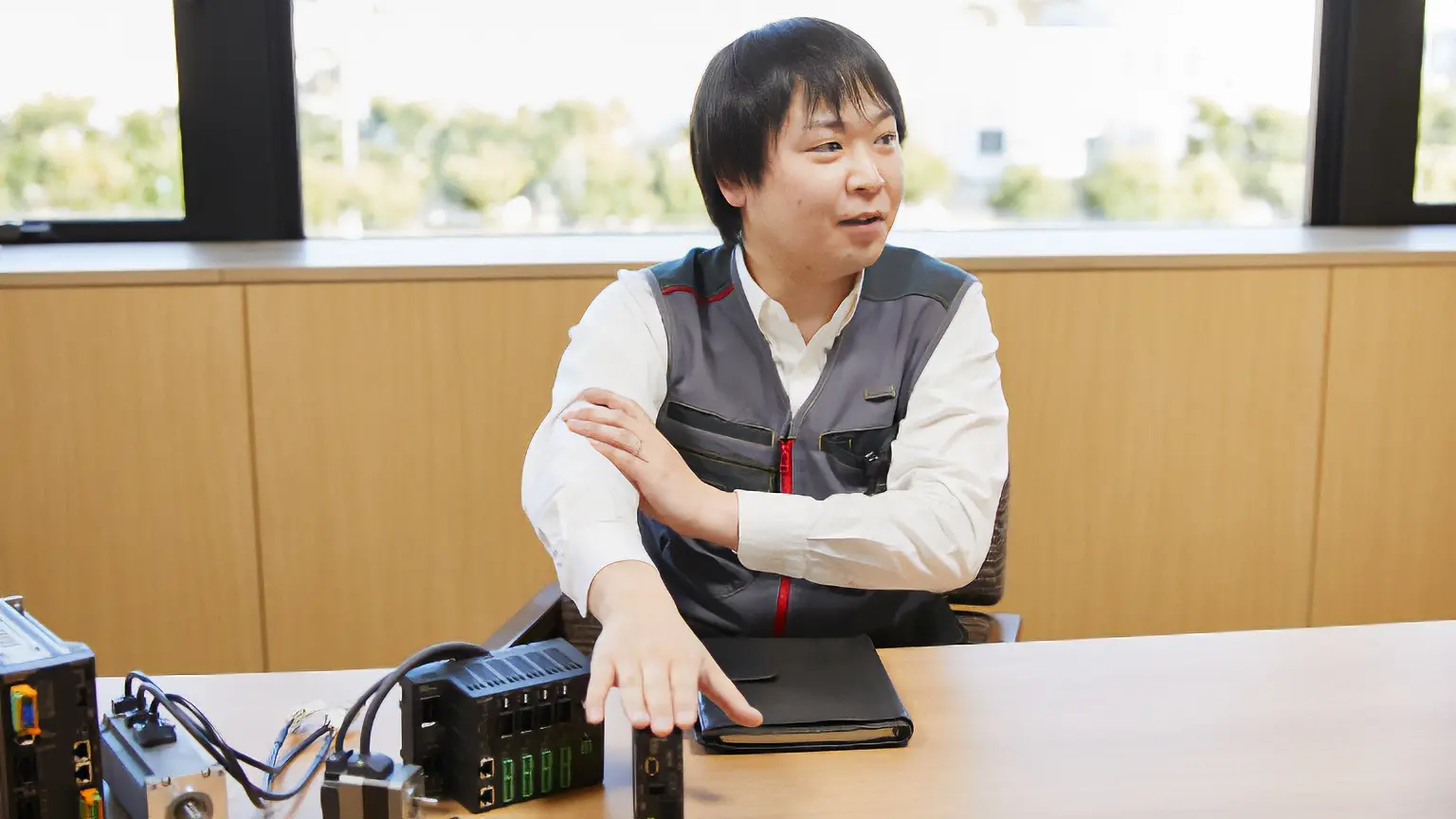
After approximately two years of development, the αSTEP AZ series was released in 2013. Since its release, with a cumulative shipment of 350,000 units in the 10 years, and approaching 1 million units for the entire αSTEP series shortly after its release, we have received high praise. ※Can you tell us about the reactions of customers at that time?
- ※ As of the end of 2021
Sugawara:With semiconductor equipment manufacturers, we received an introduction and development discussions at an early stage, so we were able to enter there as planned. In addition, customers in factory automation, such as automotive manufacturing lines, responded positively. In places with poor external conditions, such as dust or flying oil, sensors often malfunction, and we want to avoid using sensors like those for the absolute system, especially for home positions. However, with servo motors, it is challenging when the battery runs out or needs replacement. There are customers who mechanically set the return-to-home position by pressing against the mechanism end without using sensors. We learned that there are more challenges with return-to-home position setting and external sensors than we had anticipated. We believe the AZ series received high praise from such customers.
Suzuki: Initially, there were only two models, the 42 mm type and the 60 mm type, so our main activity was to introduce this new absolute system to the market. Afterward, as the lineup became more comprehensive and could cover the output range of customers, it rapidly gained popularity.
Sugawara:In fact, the previous generation αSTEP AR Series fell behind other companies in terms of network compatibility as the development couldn't keep up. Learning from that reflection, with the AZ series, we quickly deployed network-compatible features in collaboration with external partner companies. I believe that aspect was also effective in the widespread adoption of the AZ series.
Do you have any memorable episodes related to the recruitment?
Sugawara:Is this about the adoption in the wafer transport robot? Originally, the customer was using servo motors from another company, but they switched everything to our products. The decisive factor was the conveyor robot, where sensors couldn't be placed, making an absolute system essential. Due to the large load inertia and low rigidity of the mechanism, servo motors are prone to vibration and are unsuitable for such applications. It can be said that a stepper motor with closed-loop control and an absolute system was suitable. At first, as customers who had no dealings with our company, there may have been some skepticism towards us. However, now we have built a very good relationship of trust.
Are there any other points that customers appreciate?
Sugawara:Additionally, there will be considerations regarding the price range. The motor structure of stepper motors is cost-effective, and the control of the AZ series does not require high precision from the encoder. Being an absolute system, there is no need for external sensors or wiring for the home position, etc. Expect total cost reduction.
Chapter 3. Introduction of the Servo-Type AZX Series
Covering the high-output range with a servo motor. A new product designed to address the challenges of the AZ series
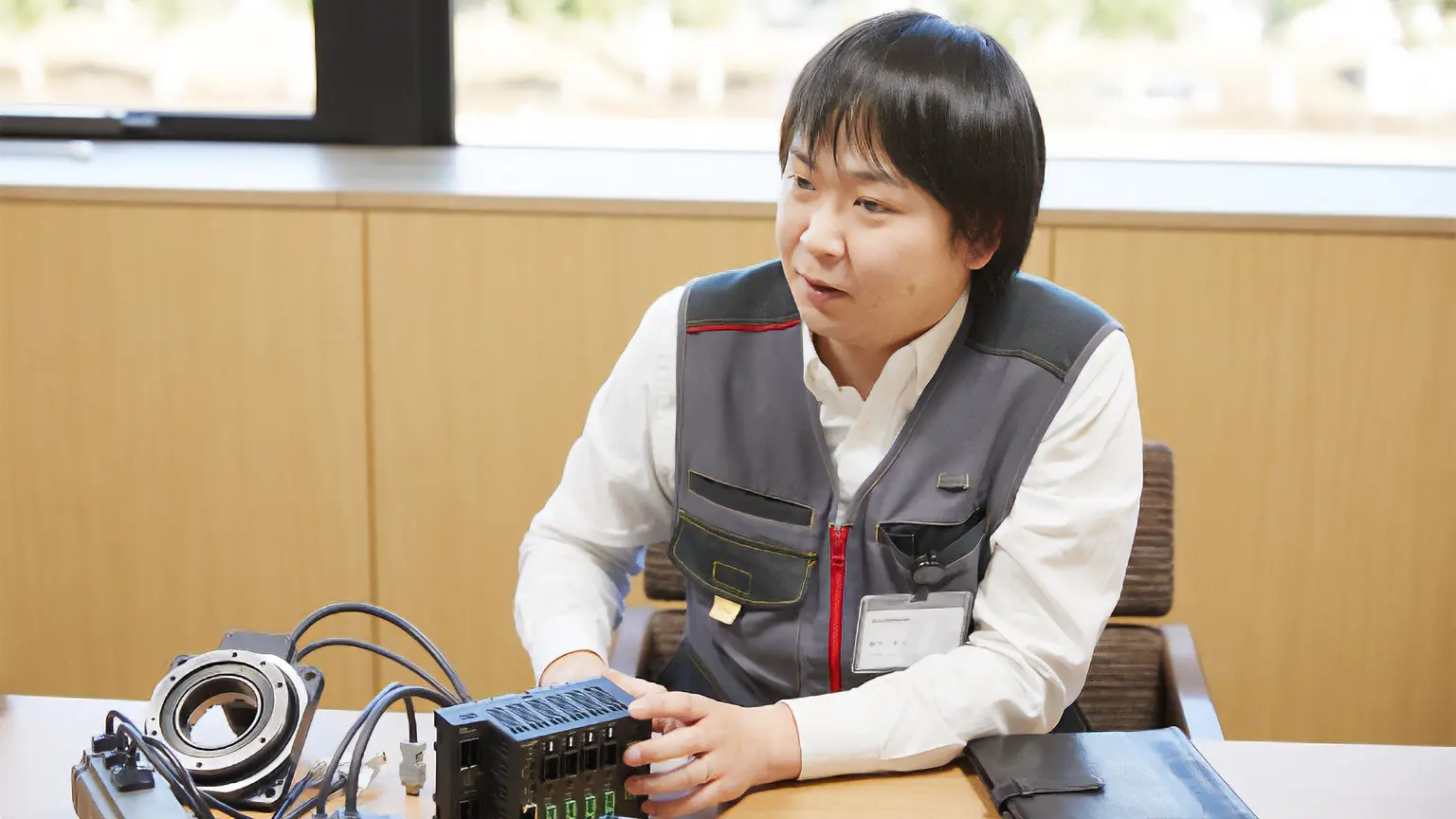
The servo-type AZX Series is joining the AZ family. Can you introduce the concept of this product?
Suzuki:Stepper motors excel in low-speed areas, so the stepper motor-based AZ series inevitably experiences a drop in torque in high-speed areas. Therefore, we haven't been able to meet the needs for larger devices or the base axis of robots, where speed and power are required. To complement this, we have introduced the AZX Series servo motor, which is now available. The AZ series, with the same interface and comparable user-friendliness, can cover the high-output range, allowing the entire system to be standardized with the AZ family. We can significantly reduce customer stress in terms of user-friendliness.
Sugawara:In the past, it was not uncommon for our products to be used for stepper motors and products from other companies for servo motors in the configuration of devices. Having different user interfaces can be burdensome for customers, so we wanted to address that issue. This product was developed with the intention of addressing that issue and making things more manageable.
Using products from another company for just one axis can still cause significant stress, correct?
Suzuki:Yes. Because software differs with each manufacturer, managing multiple systems can be a significant source of stress. Additionally, not only is the user-friendliness different, but the control characteristics also vary subtly. The way the software is programmed and the PLC can also change, so many customers are hesitant
For Oriental Motor, this is the first new servo motor product in over a decade.
Suzuki:Responding to the growing demand, we were able to commercialize the product in a relatively short period of about one year through the reuse of existing technology, starting from the planning phase. With 10 years of experience with the AZ series, we have established know-how, so despite trial and error, I think we've been able to create something good.
Sugawara:Because many of our products are small, when we first showed them to customers, there were quite a few reactions like “It's bigger than I expected.” Although it is a servo motor of a standard size, it is not exceptionally large. We will continue to provide optimal products according to the situation, making smaller things even smaller and emphasizing power where needed.
Chapter 4. Future Outlook of the AZ Family
Enhancing the AZ family and further contribute to reducing customer effort.
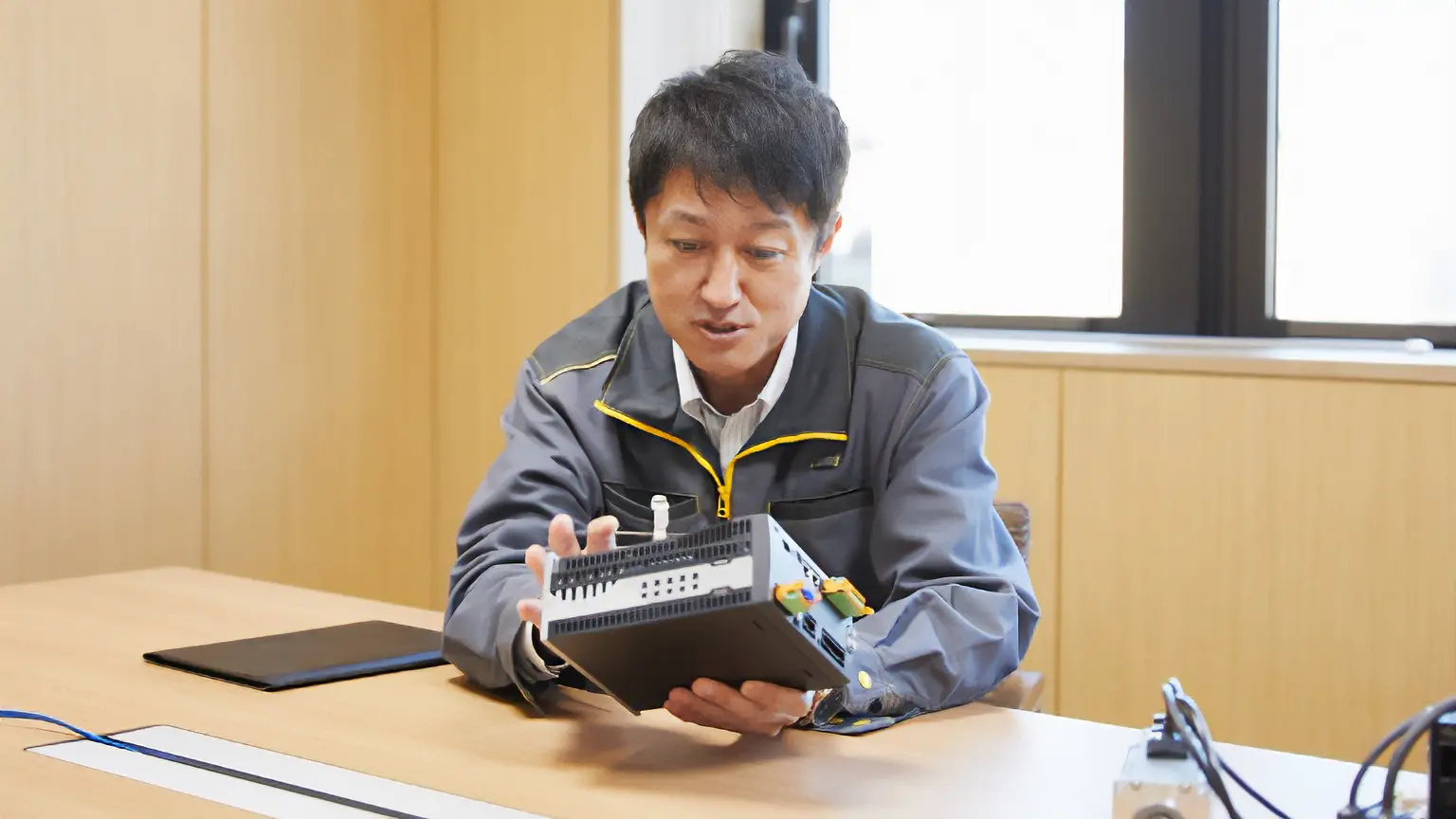
The AZ series not only includes motors but also offers products that combine gears, linear slides, cylinders, and other mechanisms as standard items in the catalog. Please tell us your intention behind that.
Sugawara:What we emphasize with our products is 'reducing the customer's effort. In other companies, it's common to use their own motors and combine them with mechanism products such as linear slides or cylinders from different manufacturers. The same applies to actuators, but on the customer's side, there is effort involved in procurement, assembly, and the evaluation of motor parameter settings, making it quite time-consuming. I want to make it usable right after installing it.
Suzuki:There are aspects of product combinations that cannot be read in the datasheet, and things often do not go as expected. Repeating the design and evaluation multiple times can be time-consuming. Products with guaranteed characteristics from the beginning are also effective in reducing man-hours.
Could you please share the future outlook for the AZ family?
Sugawara:We want to continue evolving the AZ series as the 'easiest motor for positioning in the world. We will continue to meet universal needs such as improving basic performance, miniaturization, and energy efficiency. Furthermore, by enhancing safety and reliability, we will continue to provide motion systems that can be used with confidence near humans, including the increasing number of robots, in the future. In the future, we aim to continue creating user-friendly products, emphasizing the reduction of customer effort. We look forward to further developing the AZ family.
Support for Equipment Design from the Product Selection Stage
- A full-time member of staff will select a motor on your behalf.
- Materials related to equipment specifications and dimensions of our in-house manufactured equipment are available.
For more information, please call or contact us via the web.