Brushless Motors
BLV Series
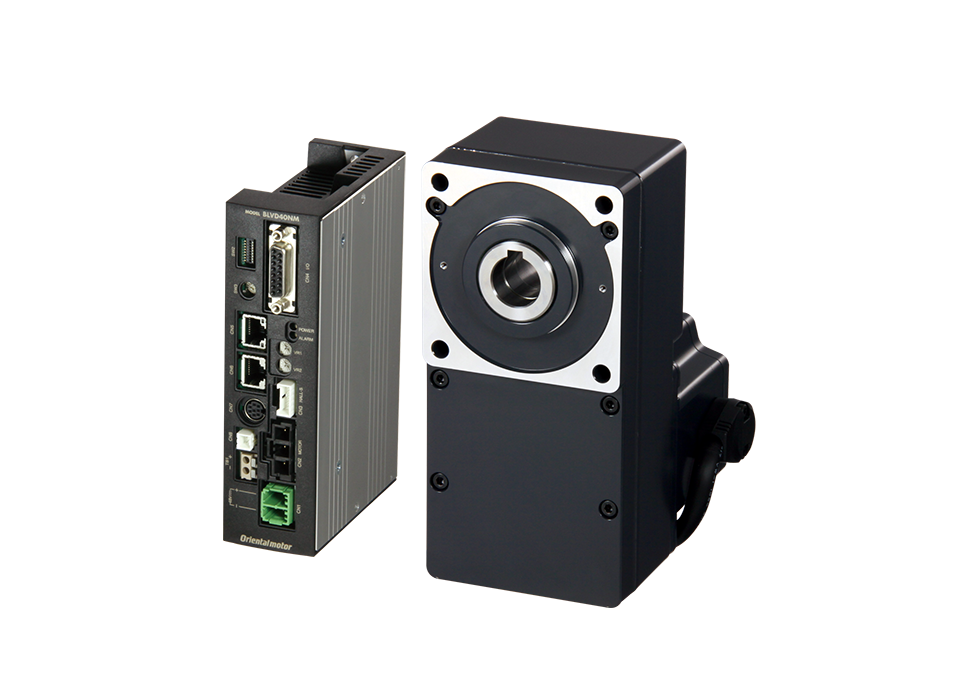
High power 100 W (0.1 kW), 200 W (0.2 kW), and 400 W (0.4 kW) DC input brushless motors.
The advantages of brushless motors, such as excellent speed stability and a wide speed control range, are retained, but supports battery operation and control via communication.
This product can also be used for AGVs including the ones used in factories and warehouses.*
Features | Brushless Motor BLV Series
Key Features
Supports Battery Drive
-
Wide Allowable Operating Voltage Range That Allows Battery Drive
As long as the voltage is within the range, the motor can be operated without triggering the alarm.
Allowable Operating Voltage Range
-
Can be Driven Even When Battery Voltage is Low
The maximum rotation speed is limited according to the voltage to avoid the motor stopping due to battery failure.
Maximum Speed Limiting Characteristics at Low Supply Voltage
Contributes to Compact, High Power Equipment Design
Hollow Shaft Flat Gearhead With High Strength and High Permissible Torque
-
High Strength
High permissible radial load enables powerful and high-spec operation.
- *200 W/400 W, 10 mm from the gearhead mounting surface
-
Unsaturated Permissible Torque
Since the permissible torque is not saturated, the motor's torque can be utilized to the fullest.
- *400 W, up to 3000 r/min
Space and Cost Saving
The hollow output shaft allows direct connection with the drive shaft.
By eliminating the need for connecting parts to the shaft, it saves space and contributes to the reduction of cost for parts.

Mechanical and Electrical Brakes Can be Used Separately or Together
Mechanical Brakes Using Electromagnetic Brakes
The electromagnetic brake type is suitable for position holding when stopped and for vertical operation (gravitational operation). When the power is turned OFF, such as during a blackout, the motor stops instantaneously to hold the load in place.
-
Vertical Operation (Gravitational operation)
-
[Stabilizes and Holds the Wheels of the AGV]
Please note that there are limitations to the power supply when using in vertical operation (gravitational operation).
Drive Method | Standard Type | Electromagnetic Brake Type | |
---|---|---|---|
Horizontal Drive | Switching-mode power supply | ○* | ○* |
Batteries | ○ | ○ | |
Vertical Operation (Gravitational operation) |
Switching-mode power supply | × | ○* |
Battery | × | ○ |
- *Regenerative energy is generated when the motor shaft is turned by an external force, such as when moving downwards on an incline or stopping suddenly. Since the driver does not have a regenerative energy processing function, the protective functions of the power supply and driver may be activated. Use a power supply or battery with sufficiently large output power capacitance and overvoltage resistance.
Generates a Holding Force When an External Force is Applied, Load Holding Function (Digital setting type, RS-485 communication type)
It can be used as an electrical holding brake* when stopping without a mechanical brake.
- *It can hold loads of up to 50 % of rated torque.
Advantages of No Mechanical Brake Mechanism
- Long life with no maintenance required due to non-wear parts
- Minimizing space usage and weight of the equipment
Note
If the power supply to the driver is turned off, the holding force dissipates. This cannot be used to prevent a fall when stopped.

Applications
Applications that frequently start and stop

Equipped With Convenient Functions for Speed Control
An Example of Other Functions
Acceleration and Deceleration Time | Acceleration and deceleration time can be set. |
---|---|
Torque limiting | This function limits the motor output torque. A TLC signal is output when the set limiting value is reached. |
Alarm | Stops operation and outputs signal Main circuit overheat/overvoltage/undervoltage/overload, etc. |
Warning | A signals is output at the warning level value before it becomes an alarm. The motor operation will continue. Main circuit overheat/undervoltage/overload, etc. |
Specification Upgrade and Expanded Functions are Available
You can extend functions in the following ways.
- Using support software MEXE02
- Using control module OPX-2A
- RS-485 communication control
- Industrial network control*1
Item | Standard Model | Expanded Model |
---|---|---|
Specifications |
|
|
Functions |
|
|
- *1
- A network converter (sold separately) is required for industrial network control.
- *2
- 100~3000 r/min for 100 W
- *3
- 80~3000 r/min for 100 W
Selectable from I/O, Modbus (RTU), and industrial network control
Control from a host controller can be performed by either I/O, Modbus (RTU), or industrial network control.
Control over the industrial network is achieved through a network converter (sold separately), which is a communication protocol converter.
I/O Control
The operation data (rotation speed, etc.) is set in advance in the driver, and signals are input from the PLC to operate at the setting data.

Modbus (RTU) Control
Easy to set operation data, parameters, and input operation commands from PLCs and other devices.

Industrial Network Control via Network Converter
This configuration uses a network converter to connect to an industrial network (sold separately). Operation data setting and operation commands input are available from the network. A single converter can connect and control multiple motors.

Support Software MEXE02 for Easy Start-Up and Maintenance
Useful Functions Utilizing Support Software MEXE02
By using the support software MEXE02, you can set and edit operation data and various parameters, as well as teach and monitor various statuses.
Click here to download the support software
Comprehensive Support From Start-Up to Maintenance With a Variety of Functions
-
Startup and Evaluation
Useful functions for wiring check and test operation are provided.
- Setting and saving of operation data
- I/O monitor
- Teaching, remote operation
-
Adjustment
The following functions are available to help you adjust motor operation after the equipment is installed.
- Waveform Monitor
-
Diagnosis and Maintenance
Diagnostic and maintenance functions are available for trouble diagnosis and maintenance after operation is started.
- Alarm monitor
- Status monitor
- Warning monitor
-
Operation Data/Parameter Setting Screen -
Waveform Monitor
Product Line
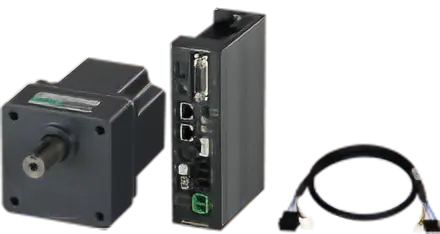

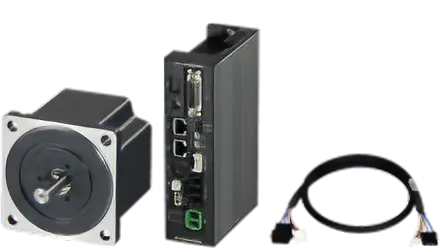
Type | Frame Size [mm] |
Rated Output Power [W] |
Maximum permissible torque*1 [N·m] |
Gear Ratio | Speed Control Range [r/min] |
Electromagnetic Brake |
---|---|---|---|---|---|---|
Parallel Shaft Gearhead GFS Gearhead | 90 | 100 | 30 | 5~200 | 100 (80)*3 ~3000 |
Equipped/Not equipped |
104 | 200 | 63 | 5~200 | 100 (80)*3 ~4000 |
||
400 | ||||||
Hollow Shaft Flat Gearhead FR Gearhead | 90 | 100 | 54 | 5~200 | 100 (80)*3 ~3000 |
|
104 | 200 | 38.3 | 10~100 | 100 (80)*3 ~4000 |
||
400 | 80.8 | 5~100 | ||||
Round Shaft Type | 104 | 200 | 0.65*2 | - | 100 (80)*3 ~4000 |
|
400 | 1.3*2 |
- *1
- The value for permissible torque is the value at the maximum rotation speed.
- *2
- The value for the round shaft type is the rated torque (N·m).
- *3
- These specifications apply when using digital settings (support software MEXE02, control module OPX-2A) or setting via communication.
Gearhead is Removable
The gearhead can be removed to change the direction of the motor cable outlet direction. It is also possible to replace only the gearhead when the gear ratio of the gearhead needs to be changed.
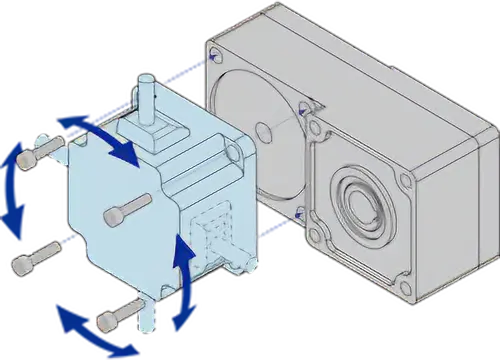
Significantly Increases Permissible Load Flange Drive Adapter (Sold separately)
Mounting on a parallel shaft gearhead increases permissible radial and axial loads.

Related Products
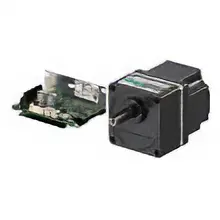
Brushless Motor BLH Series
This is a brushless motor that uses a 24 VDC board type driver, ideal for equipment that requires space saving.
Output Power: 15 W~100 W
Speed Control Range: 100 (80)~3000 r/min
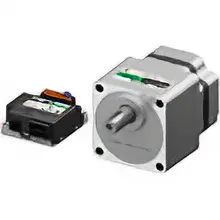
Brushless Motor BLV Series R Type
A brushless motor with DC input that achieves high power and compact size.
This helps in the development of even more compact battery drive devices.
Output Power: 60 W, 100 W, 200 W, 400 W
Speed Control Range: 1~4000 r/min
Download
Operating Manual
Support Software
Lineup and Related Information
Combining with Other Manufacturers' Products